Section
Data-Driven Manufacturing with Dynamics 365 for Predictive Maintenance & Quality Assurance
Section
Table of Contents
- The Role of Dynamics 365 in Data Driven Manufacturing
- Predictive Maintenance with Dynamics 365
- Quality Assurance Enhancements through Dynamics 365
- Streamlining Supply Chain Operations
- Advanced D365 MES Integration
- Implementation Best Practices
- Enterprise Success Stories on Data Driven Manufacturing with Dynamics 365
- Conclusion
Section
In this comprehensive overview, we delve into how Dynamics 365 empowers data-driven manufacturing, specifically focusing on predictive maintenance and quality assurance. We’ll explore the transformative capabilities of integrating real-time data analytics, which allow manufacturers to anticipate maintenance needs and uphold stringent quality standards. Discover how leveraging these insights not only minimizes downtime but also boosts operational efficiency and product quality across the manufacturing floor. This synopsis encapsulates the strategic advantage of adopting Dynamics 365 for a proactive, data-informed manufacturing approach.
The manufacturing industry is currently undergoing continuous transformation driven by the proliferation of advanced digital technologies and evolving safety, compliance, and quality standards. Microsoft Dynamics 365 supports this shift, enabling data-driven manufacturing processes that significantly boost efficiency and productivity across extensive enterprise-scale operations. The platform’s recent enhancements include advanced AI and data solutions that transform traditional manufacturing environments into sophisticated, interconnected systems. These updates facilitate data unification and real-time analytics, which are essential for enhancing operational agility and refining decision-making processes.
In heavy manufacturing, the adoption of technologies offered by Dynamics 365 is particularly impactful due to the complexity and scale of operations in this sector. The platform enhances capabilities in predictive maintenance and quality assurance, enabling manufacturers to anticipate potential issues and consistently uphold high-quality standards. Moreover, the integration of real-time data analytics and AI-driven insights optimizes supply chains and production lines, reducing downtime and increasing output. This strategic deployment of Dynamics 365 not only meets the industry’s demands for agility and sustainability but also drives innovation and growth in a fiercely competitive market.
Here’s how Dynamics 365 is revolutionizing the industry:
- Integration with Existing Systems: Dynamics 365 seamlessly integrates with current manufacturing setups, ensuring that there’s minimal disruption while transitioning to more advanced systems.
- Holistic Operational Improvement: By combining predictive maintenance and quality assurance, Dynamics 365 offers a comprehensive solution that addresses multiple aspects of manufacturing operations from a single platform.
- Data Utilization: At the core of Dynamics 365’s effectiveness is its ability to harness data from various sources across the manufacturing process, enabling more informed decision-making and strategic operational adjustments.
The Role of Dynamics 365 in Data Driven Manufacturing
Microsoft Dynamics 365 is reshaping manufacturing industries by integrating critical business processes with advanced digital tools. Here is a deeper look at the transformative impact of Dynamics 365 in the manufacturing sector:
- Capabilities Tailored for Industry Needs: Dynamics 365 offers specialized capabilities designed to meet the unique demands of the manufacturing sector. This includes everything from resource planning and supply chain management to customer engagement and service optimization.
- Enhanced System Integration: The platform facilitates a seamless connection between existing manufacturing quality assurance systems and advanced digital solutions, promoting an efficient and cohesive operational environment. This integration supports real-time data exchange and process automation, crucial for timely decision-making and responsiveness.
- Holistic Approach for Operational Excellence: By merging predictive maintenance, quality assurance, and manufacturing execution systems (MES), Dynamics 365 enables manufacturers to adopt a comprehensive approach to operational management. This holistic strategy not only streamlines various manufacturing processes but also boosts overall productivity and system reliability.
Key Points:
- Integration Benefits: Enhanced connectivity between systems leading to improved data accuracy and operational efficiency.
- Predictive Maintenance: Proactive maintenance strategies supported by real-time data analytics to prevent downtime and extend equipment life.
- Quality Assurance Tools: Advanced tools for consistent quality checks, ensuring product reliability and compliance with standards.
Section
Section
Incorporate Dynamics 365, Transform Manufacturing
Predictive Maintenance with Dynamics 365
Predictive maintenance is a pivotal aspect of modern manufacturing, ensuring equipment reliability and optimizing maintenance schedules. Microsoft Dynamics 365 leverages IoT and AI technologies to transform how predictive maintenance is implemented in the manufacturing industry.
Key Features of Predictive Maintenance with Dynamics 365:
- IoT and AI Integration: Dynamics 365 utilizes IoT sensors to continuously monitor equipment and gather data. This data is then analyzed using AI algorithms to predict potential equipment failures before they occur.
- Proactive Maintenance Scheduling: By predicting when maintenance should occur, Dynamics 365 helps manufacturers avoid unplanned downtime, which can be costly and disruptive. This proactive approach not only saves time but also extends the lifespan of machinery.
Benefits to Manufacturers:
- Reduced Downtime: Minimizing unexpected breakdowns leads to more consistent production and operations.
- Extended Equipment Lifespan: Regular maintenance based on predictive data can enhance the durability and performance of machines.
- Cost Savings: Efficient maintenance scheduling reduces the need for emergency repairs and spare parts inventory.
Dynamics 365’s predictive maintenance capabilities are designed to be straightforward and integrate seamlessly into existing workflows, thereby enhancing the efficiency and reliability of manufacturing quality assurance. This technology not only supports operational excellence but also drives significant cost savings and operational improvements for manufacturers.
Quality Assurance Enhancements through Dynamics 365
Quality assurance (QA) is integral to maintaining high standards in manufacturing, ensuring that products meet stringent requirements before reaching the market. Dynamics 365 enhances QA processes by integrating advanced digital tools that streamline operations and improve product consistency.
Key Aspects of Quality Assurance with Dynamics 365
- Automated Quality Checks: Dynamics 365 facilitates automated inspections and quality checks, reducing human error and increasing efficiency. This automation supports consistent quality across production batches, crucial for industries where precision is paramount.
- Data-Driven Quality Insights: The platform provides comprehensive analytics tools that allow manufacturers to monitor and analyze quality data in real-time. This capability enables timely adjustments in the production process, enhancing overall product quality.
Impact on Manufacturing
- Improved Product Consistency: Automated systems ensure products are manufactured to exact specifications, reducing variability, and enhancing customer satisfaction.
- Enhanced Compliance: Dynamics 365 helps manufacturers adhere to industry regulations and standards, mitigating risks associated with non-compliance.
- Customer Satisfaction and Brand Reputation: High-quality products bolster customer trust and enhance the manufacturer’s reputation in the market.
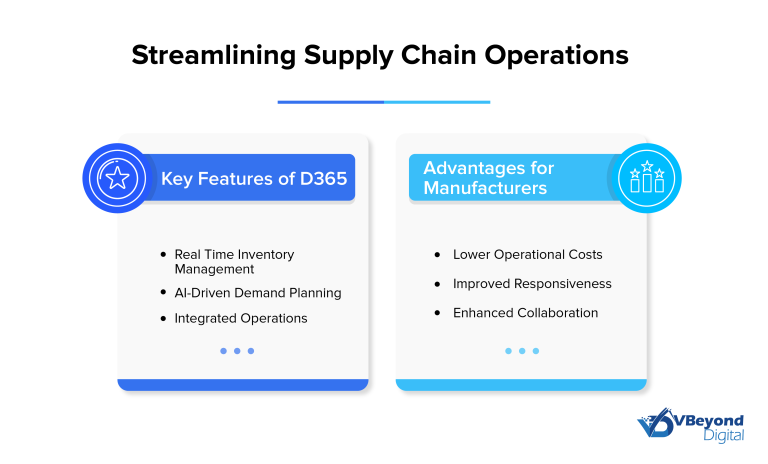
Streamlining Supply Chain Operations
Dynamics 365 significantly enhances supply chain management by integrating sophisticated features that enable real-time visibility and proactive management of supply chain activities. This integration not only reduces operational costs but also improves responsiveness to market demands and production needs.
Key Features of D365 Supply Chain Management
- Real Time Inventory Management: Dynamics 365 Supply Chain Management offers tools that provide real-time insights into inventory levels, enabling better stock control and reducing the likelihood of overstocking or stockouts.
- AI-Driven Demand Planning: Advanced AI algorithms help predict future demand more accurately, allowing companies to adjust their production schedules and inventory levels accordingly. This capability is crucial for maintaining efficient operations and meeting customer expectations.
- Integrated Operations: The platform supports a unified approach to managing supply chain processes, from procurement to production to distribution. This integration helps streamline operations, minimize delays, and reduce costs.
Advantages for Manufacturers
- Lower Operational Costs: Efficient management of resources leads to reduced waste and lower storage costs.
- Improved Responsiveness: Quick adaptation to changes in demand or supply conditions ensures that operations remain efficient, and customer needs are consistently met.
- Enhanced Collaboration: Dynamics 365 facilitates better collaboration across various departments and external partners, improving overall supply chain performance.
Advanced D365 MES Integration
Integrating Manufacturing Execution Systems (MES) with Dynamics 365 offers substantial improvements in manufacturing operations, enabling a more synchronized and data-coherent environment between production and enterprise levels. This integration is critical for achieving real-time visibility and control over the manufacturing processes.
Key Benefits of D365 MES Integration
- Seamless Data Exchange: Dynamics 365 facilitates the smooth transfer of data across different systems within the manufacturing environment, ensuring that all parts of the organization have up-to-date information.
- Process Synchronization: By integrating MES, Dynamics 365 helps synchronize production operations with business processes, aligning manufacturing activities with broader corporate objectives.
- Enhanced Visibility: Real-time data provided by MES integrated with Dynamics 365 allows for better monitoring of the production floor, helping to identify bottlenecks and inefficiencies promptly.
Impact on Manufacturing Operations
- Improved Data Accuracy: Accurate, real-time data reduces errors and enhances decision-making, leading to more efficient operations.
- Streamlined Operations: Integration minimizes disruptions and delays, enhancing workflow efficiency and productivity.
- Better Resource Utilization: Effective synchronization of production and planning processes ensures optimal use of resources, reducing waste and costs
Implementation Best Practices
Implementing Dynamics 365 in a manufacturing setting involves strategic planning and careful execution. Here are best practices to ensure a successful deployment:
Key Considerations for Dynamics 365 Implementation:
- Comprehensive Planning: Begin with a detailed analysis of your current processes and systems to identify areas that will benefit most from Dynamics 365. This planning phase should involve key stakeholders and end-users to ensure the solution meets the actual needs of the organization.
- Phased Deployment: Implement Dynamics 365 in stages rather than all at once. This allows for manageable transitions, easier troubleshooting, and better adoption across the organization.
- Training and Support: Provide extensive training and resources to your staff. Effective use of Dynamics 365 requires users to be well-versed in the features relevant to their roles.
Steps for Successful Deployment:
- System Configuration: Tailor Dynamics 365 to align with specific business processes and requirements.
- Data Migration: Migrate data from existing systems carefully to avoid loss or corruption. Validate and clean data before and after transfer.
- Testing and Feedback: Conduct thorough testing of the system to identify any issues. Use feedback from users to make necessary adjustments.
Best Practices for Real Time Inventory Management:
- Engage Expertise: Utilize the expertise of certified Dynamics 365 professionals to guide the implementation process.
- Continuous Evaluation: After implementation, continually assess the system’s performance and user satisfaction to identify areas for improvement.
Enterprise Success Stories on Data Driven Manufacturing with Dynamics 365
Exploring real-world applications of Dynamics 365 in manufacturing provides valuable insights into its effectiveness and the transformative impact it can have on operations. Below are case studies that highlight successful implementations, and the results achieved.
Case Study 1: ChemTreat
Problem: ChemTreat struggled with a legacy ERP (Enterprise Resource Planning) system that was not only outdated but also restrictive, hindering their growth and operational efficiency. The old system was desktop-bound, required nightly downtime, and kept data trapped in spreadsheets, making it difficult to manage their expanding operations effectively.
Solution: ChemTreat implemented Dynamics 365 Supply Chain Management to modernize their ERP system. This transition to Dynamics 365 allowed for real-time, end-to-end supply chain visibility and integrated smoothly with their existing operations.
Benefits: The upgrade to D365 Supply Chain Management enabled ChemTreat to proactively manage raw material shortages and enhance their planning and execution processes. It also supported their growth ambitions by providing a scalable solution that improved service delivery and operational flexibility. The result was not only enhanced operational efficiency but also significant improvements in customer service and satisfaction (Microsoft Cloud).
Case Study 2: Daimler Trucks North America (DTNA)
Problem: DTNA faced challenges in meeting customer demands due to inadequate supply chain visibility and responsiveness. The complexity of managing a global supply base and the need for accurate delivery schedules were paramount.
Solution: DTNA adopted Dynamics 365 Supply Chain Insights, integrating AI-driven Microsoft supply chain management tools that provided early visibility into potential supply constraints and enabled real-time data sharing with suppliers.
Benefits: This strategic implementation allowed DTNA to improve logistics costs by 15%, inventory levels by 35%, and service levels by 65% compared to competitors. The enhanced visibility and predictive capabilities of Dynamics 365 helped DTNA make more informed decisions, reduce operational disruptions, and provide accurate delivery dates, thus significantly improving overall supply chain efficiency and customer satisfaction (Microsoft Cloud).
Conclusion
Throughout this exploration, we’ve delved into how Dynamics 365 enhances data driven manufacturing processes through innovative integration of predictive maintenance and quality assurance. These capabilities not only streamline operations but also foster significant improvements in efficiency, reliability, and quality.
As the manufacturing sector continues to evolve, embracing advanced solutions like Dynamics 365 becomes essential. For senior executives considering a digital transformation, Dynamics 365 offers a robust platform that not only addresses current operational challenges but also positions businesses for future growth and innovation.